It’s important to test SF6 gas inside GIE (Gas Insulated Equipment) because it ensures the safety of the operator and protects the equipment from damage. When an SF6 gas sample is taken from a piece of equipment, it is compared against the manufacturers specifications in order to verify if the gas and the equipment is in an acceptable range of health. If you are unsure whether or not the equipment has any contaminants, it is safest to assume it does. Any arcing events (generating heat > 380°F) will create byproducts, therefore all operators working on GIE that has been previously installed should follow all recommended safety precautions.
SF6 Gas Test Methods
There are three commonly used methods to test the gas; on-site testing using a field level analyzer, lab analysis & online monitoring. Manufacturer specifications, governmental/organizational requirements, and other factors will determine what method is used. Each method has varying degrees of precision, efficiency and costs that make choosing the right method important. For the purpose of this article, we will focus on using a field level analyzer.
Avoiding Contaminants
Before delving into how to perform a tests, it is important to take a quick step back and look at how to properly handle the SF6 being analyzed. Remember, the results of the analysis are only as good as the sample you provide the measuring device. Since almost everything we work with contains water, much of the focus will be placed on avoiding this contaminant.

Using the correct materials is vital to obtaining an accurate moisture sample. Generally speaking, the materials normally used to handle SF6 do not have an impact on purity or arc byproduct sampling. While it is okay to handle SF6 with parts containing rubber, such as hoses, it is a major source of moisture contamination for the small volumes of SF6 used for analysis and MUST be avoided. Sampling hoses are typically made out of a Teflon type material with stainless steel fittings. It is also important that regulators used contain stainless steel, Hastelloy or brass diaphragms. Some common handling errors can also have a negative impact. This includes:
- Mishandling sampling equipment, hoses, & fittings. Sweat from someone’s fingers getting onto the surface of a fitting can cause a massive spike in moisture.
- Leakage on a hose or fitting can also introduce moisture into a sample. On certain devices, it can also lead to a reduction in gas purity.
- Testing when ambient temperatures are too low can lead to false dry readings.
Before You Start, Is Your Device Operating Correctly?
Whether reviewing leaflets for new devices or trying to verify that existing units are performing properly, it is very important to understand the specifications for each type of sensor that an analyzer uses. The tolerances for each type convey what is expected when measuring against a known value. Our “known values” are certified gasses that are used to verify proper functionality of test equipment of any kind. It should be noted that these gasses also have a tolerance. On most certificates you will see “Analytical Result(s)” and + 2% to 10% of the result shown. Refer to sample sheet below:

Let’s look at some examples of some advertised sensor tolerances and what the resulting reading on the device should be giving if measuring against a calibration gas:
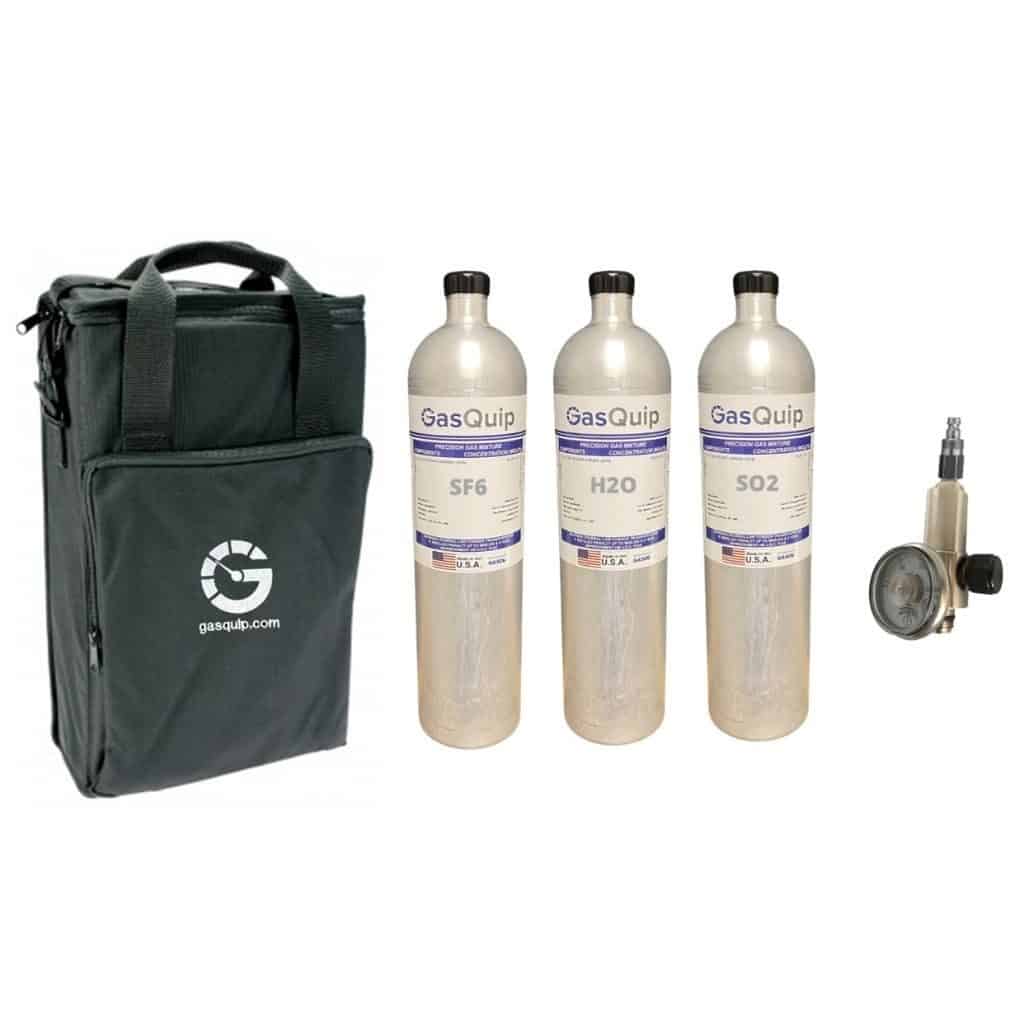
Gas Volume Percentage (%)
Advertised Sensor Tolerance: + 0.5%
- Example Test: Calibration gas cylinder that is certified at an SF6 Volume percentage of 98.00 %. The readings on the device should be between 97.5% to 98.5%. If the readings are outside of this range, then your sensor needs service.
Decomposition Products (SO2, HF, CF4, H2S, CO, etc.) (ppmV)
Advertised Sensor Tolerance: + 2% Full-Scale Reading, 0-500 ppmV range
- Example Test: Calibration gas cylinder that is certified at 200 ppmv SO2. At 2% (of 500), your sensor’s tolerance is ±10 ppmV. So if you test the sensor against that calibration gas and it does not read within 190-210 ppmV, the sensor is out of tolerance.
H2O (Dew Point °C )
Advertised Sensor Tolerance: + 2°C with range of -60ºC to ±20ºC
- Example Test: Calibration gas cylinder that is certified at -36ºC . Your analyzer needs to read between -34ºC & -38ºC. If it does not read within those limits, the sensor is out of tolerance.
*Note that many analyzers use ppmV instead of dewpoint. These two units share a non-linear relationship, and you can use the below chart to convert between the two:

Testing at the GIE
Once you have confirmed that your analyzer is working properly, it’s time hook up to the gas compartment on the GIE and run a test. Here is a free excerpt from our online training that demonstrates how to properly operate an SF6 analyzer:
Testing a Cylinder of SF6 Gas
While the methods for testing SF6 cylinders and circuit breakers is the same, the behavior of moisture in each is drastically different. In a breaker, the gas is always in vapor form, so the readings will tend to be quite stable and repeatable. In a cylinder, however, the opposite is true. Cylinders generally contain both liquid and vapor. The vapor portion on top of the liquefied gas is referred to as the head or vapor space.

Moisture tends to hang out in the headspace inside bottles. This is the main reason there are two different standards for SF6 in cylinders, one for liquid (ASTM) & another for the vapor phases (CIGRE). Field level devices cannot test from the liquid phase, so standards applying to the headspace must be used.
When testing the vapor space, the first test will normally be the wettest. Each test after that performed in sequence will be dryer with each test. This happens due to two reasons: 1) dry SF6 is vaporizing and diluting the moisture levels. 2) a tremendous energy loss occurs when SF6 vaporizes causing a temperature drop which makes the moisture condensate then freeze.
General Tips
Gas Analyzers with Pump Back Systems:
- Pump back feature only works up to a maximum of 145 psig
- It cannot pump back into cylinders with liquefied SF6 inside
- Regulators only allow gas flow one way. It is not possible to pump back through a regulator.
- Before pumping sample gas back into a breaker, make certain no additional tests are needed that day. Retesting SF6 after pump-pump back will result in an incorrect moisture reading, normally a sharp increase. It is only a small amount of moisture introduced, but it takes time for the gas to re-homogenize. Wait at least 24 hours.
- Analyzers with pump back feature hold 2-3 samples. If additional testing is necessary on the same gas volume, have a gas recovery bag available to empty the device into before pumping back.
Other General Notes:
- Do not use Loctite/liquid thread sealant on any fittings used for sampling SF6. Chemical off-gassing can foul test equipment.
- It is normal for moisture values to decrease on cylinders when performing multiple tests in a row. This is caused by the cooling of the gas during vaporization and very dry gas entering the vapor space.
- Always make sure your device is charged before heading out to a jobsite.
Confused? Need equipment, training, or advice? Contact us at sales@gasquip.com so we can help!